In statu nascendi – Auf dem Weg zur Herstellung von Autoinjektoren in der Bundeswehr
A. Rohe, R. Müller-Pfaff
Morphin-Autoinjektoren sind ein wesentlicher Bestandteil der Gefechtsfeldanalgesie. Gleichermaßen sind Atropin-Autoinjektoren, gegebenenfalls in Kombination mit Oximen, aus der Selbst- und Kameradenhilfe bei Kampfstoffvergiftungen mit Organophosphaten nicht wegzudenken. Diese und weitere wehrmedizinisch relevante Einsatzfelder in Verbindung mit der unsicheren Marktverfügbarkeit militärisch nutzbarer Autoinjektoren führten zur Entscheidung, eine Eigenherstellung von Autoinjektoren in der Bundeswehr zu etablieren. Hierbei handelt es sich um eine erlaubnispflichtige Herstellung im Sinne des Arzneimittelgesetzes. Die Bundeswehrkrankenhausapotheke Ulm ist neben dem Blutspendedienst der Bundeswehr eine der beiden bestehenden Betriebsstätten der Bundeswehr für die Großherstellung von Fertigarzneimitteln. Die auf dem bisherigen Produktportfolio basierende Erfahrung in der Herstellung steriler flüssiger Arzneiformen führte zur Entscheidung, die Autoinjektoren am Standort Ulm zu fertigen. Derzeit läuft die Realisierungsphase.
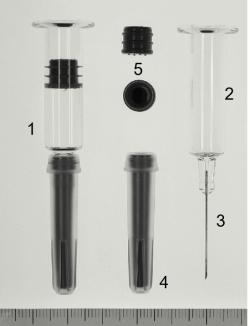
Die Etablierung der Eigenherstellung stellt ein durchweg komplexes Unterfangen dar. Zu betrachten ist dabei zunächst einmal der Autoinjektor selbst: Was muss er können, welche Einzelteile sind dafür nötig, wie müssen diese beschaffen sein und wie zusammenwirken? Hier besteht zwangsweise eine enge Verzahnung mit dem Kommando Sanitätsdienst der Bundeswehr als dem für die Erfüllung der regulatorischen Anforderungen verantwortlich zeichnenden Pharmazeutischen Unternehmer. Denn was nützt der beste Autoinjektor, wenn er keine Zulassung erhält und in der Folge nicht ausgeliefert werden darf? Schon frühzeitig müssen daher zulassungsrelevante Daten, Informationen und Ergebnisse zusammengestellt werden, um die hohen Hürden einer nationalen Arzneimittelzulassung später überwinden zu können. Spezielle Daten zur pharmazeutischen Qualität sowie Stabilitätsdaten werden dabei vom Zentralen Institut des Sanitätsdienstes der Bundeswehr München beigesteuert. Die Autoinjektorherstellung erfordert zudem neue Maschinen, deren Beschaffung über das Bundesamt für Ausrüstung, Informationstechnik und Nutzung der Bundeswehr erfolgt und eng mit den infrastrukturellen Voraussetzungen abgestimmt sein muss. Nicht zuletzt kommt der Gewinnung und auch der Qualifizierung von Fachpersonal besondere Bedeutung zu, um diese neuen, fordernden Aufgaben fach- und zeitgerecht ausführen zu können.
Funktionsweise des künftigen Autoinjektors der Bundeswehr
Das Herzstück des Autoinjektors ist eine sogenannte Fertigspritze, also ein Glaszylinder mit eingeklebter Edelstahlkanüle (siehe nebenstehende Abbildung). Die Kanüle ist mit einem Nadelschutz versehen, der zugleich als ausstoßseitiger Stopfen fungiert und das Auslaufen der Flüssigkeit verhindert. Die Arzneistofflösung wird in die Fertigspritze gegeben und mit einem Kolbenstopfen verschlossen. Diese vorgefüllte Fertigspritze wird anschließend in die Autoinjektorhülle eingebracht, welche selbst ein komplexes Medizinprodukt der Klasse IIb im Sinne der einschlägigen EU-Verordnung ist. Die Hülle nimmt die mit Arzneistofflösung vorgefüllte Fertigspritze auf und wird damit rechtlich zu einem Arzneimittel. Im weiteren Verlauf der Fertigung wird die Fertigspritze im Innern der Autoinjektorhülle in eine Art Schlitten eingesetzt und eine Kolbenstange in die lösungsabgewandte Seite des Kolbenstopfens geschoben. Der Nadelschutz rastet irreversibel in eine Aufnahme in der Nadelschutzkappe ein, so dass bei Anwendung des Autoinjektors durch Abziehen der Kappe gleichzeitig der Nadelschutz abgezogen wird. Die freiliegende Kanüle ist zu diesem Zeitpunkt noch im Innern des Autoinjektors und für den Anwender nicht sichtbar.
Im Gegensatz zu den bereits in die Truppe eingeführten Autoinjektoren ist die abzuziehende Autoinjektorkappe an der Nadelseite aufgesetzt und nicht auf der gegenüberliegenden Seite. Daraus ergibt sich der Vorteil, dass auf eine zusätzliche Folienverpackung verzichtet und der erforderliche Schutz von Mechanik und Spritzenkörper über die Autoinjektorhülle in Verbindung mit einer großflächigen Etikettierung sichergestellt werden kann. Das Etikett trägt wesentlich zur Funktionalität des Autoinjektors bei. Die NATO-konforme Farbkodierung (rot – Morphin, gelb – Atropin, etc.) und Infrarotlesbarkeit (Nachtsicht) werden neben den rechtlich verpflichtenden Angaben darauf aufgebracht. Zudem können Relieflacke und Antirutschbeschichtungen die Griffigkeit des Autoinjektors und damit dessen Handhabung auch unter taktischen Bedingungen verbessern. Die Etikettierung des umlaufenden Öffnungsspalts an der Kappe sowie montagebedingter Spaltöffnungen führt zu einem erheblich verbesserten Schutz gegenüber Umwelteinflüssen (Schmutz, Feuchtigkeit, Chemikalien). In Verbindung mit seiner Eigenschaft als Manipulationsschutz, mit dem das Öffnen der Kappe sicher erkannt werden kann, wird durch das Etikett die Verwendung einer zusätzlichen Verpackung vollends überflüssig. Der Einsatz unter Gefechtsbedingungen wird durch die Gestaltung des Autoinjektors deutlich erleichtert und beschleunigt.
Das Abziehen der Kappe durchtrennt eine Perforationslinie des Etiketts irreversibel und sorgt neben der Entfernung des Nadelschutzes im Autoinjektor zugleich für die Scharfschaltung des Auslösemechanismus. Kräftiges Aufsetzen an der gewünschten Injektionsstelle löst den Autoinjektor dann aus: Im Innern wird der Schlitten mit der vorgefüllten Fertigspritze mit einem Federmechanismus nach vorne geschoben. Die Nadel penetriert dabei die Haut bis in darunterliegende Muskelschichten. Nach Ende des Vorschubvorgangs beginnt die Ausstoßphase. Angetrieben durch einen zweiten Federmechanismus wird der Kolbenstopfen mithilfe der Kolbenstange nach vorne geschoben und die enthaltene Arzneistofflösung vollständig durch die Kanüle in den Muskel gedrückt. Beim Herausziehen der Nadel fährt eine farbige, sogenannte passive Nadelschutzvorrichtung aus, sodass bei Anwendung während des gesamten Vorgangs nie eine freiliegende Kanüle zu sehen ist und damit zu keinem Zeitpunkt die Gefahr einer unbeabsichtigten Verletzung besteht. Durch die klar erkennbare farbige Nadelschutzvorrichtung mit eingeschmolzenen infrarotsichtbaren Pigmenten kann ein ausgelöster Autoinjektor in praktisch jeder Situation sicher von einem nicht ausgelösten und damit voll funktionsfähigen Autoinjektor unterschieden werden.
Abgesehen von der bedarfsgeleiteten Wirkstoffauswahl unterscheidet sich der militärisch genutzte Autoinjektor von seinem zivilen Gegenpart in wesentlichen Punkten, die nicht alleine nur seine olivgrüne Grundfarbe betreffen. So sind die Anforderungen an Robustheit und Lagerstabilität im militärischen Umfeld ungleich höher. Tiefe intramuskuläre Injektion durch mehrere Kleiderschichten hindurch ist erwartungsgemäß im zivilen Umfeld unüblich. Dies hat aber erhebliche Auswirkungen auf beispielsweise Nadellänge und den Schliff der Kanülenspitze. Ergänzend zu den arzneimittelrechtlich vorgeschriebenen Kennzeichnungselementen sind auch Forderungen der NATO zu beachten.
Geplanter Herstellungsprozess
Der geplante Prozess der Autoinjektorherstellung ist vereinfacht in der folgenden Abbildung dargestellt.
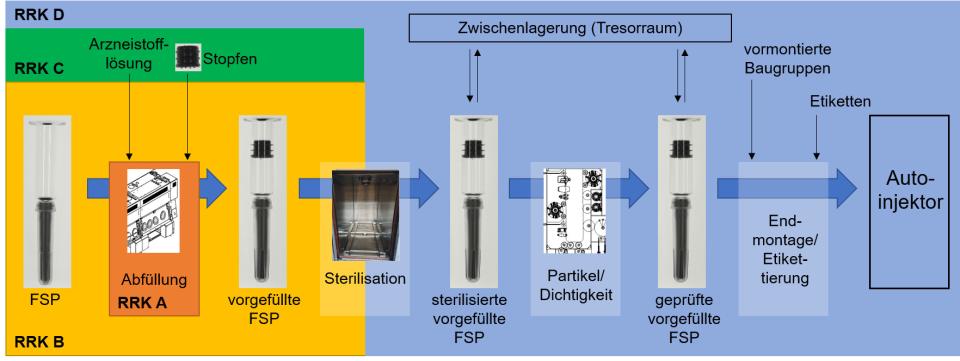
Die Herstellung erfolgt in Reinräumen, welche strengen Grenzwerten für Mikroorganismen und Raumluftpartikel unterliegen. Je nach Reinheit sind dies abgestuft die Reinraumklassen (RRK) A bis D, wobei RRK A die reinste Stufe darstellt. Auf dem Weg zur RRK A darf keine Klasse übersprungen werden, es müssen alle davorliegenden Klassen durchlaufen werden. Die sterile, zu befüllende Fertigspritze wird in einen Raum der RRK B eingeschleust und einer Spritzenfüll- und -verschließmaschine zugeführt. In ihr erfolgt dann die Abfüllung der zuvor aufwendig hergestellten Arzneistofflösung. Diese wird dazu aus einem angrenzenden Reinraum heraus in den Abfüllraum und von dort in die Maschine, in deren Abfüllbereich die höchste RRK A gewährleistet sein muss, eingebracht. Ist die Fertigspritze mit Arzneistofflösung beschickt, wird der vorsterilisierte und in den Abfüllbereich eingeschleuste Kolbenstopfen blasenfrei unter Anlegen von Unterdruck in der Fertigspritze positioniert. Die vorgefüllte Spritze wird von der Maschine ausgeworfen und mittels eines Durchreichedampfsterilisators hitzesterilisiert. Nach Entnahme der sterilisierten, vorgefüllten Fertigspritzen von der gegenüberliegenden Seite kann diese sogenannte Halbfertigware zwischengelagert werden. Im Falle des Wirkstoffs Morphin muss die Zwischenlagerung unter besonderen Sicherheitsmaßnahmen in einer Art Tresorraum erfolgen, da es sich um ein Betäubungsmittel handelt. In der Folge werden die Fertigspritzen unabhängig vom Wirkstoff einer automatisierten optischen Prüfung auf Partikel unterworfen. In diesem Verfahren wird zugleich mithilfe eines angelegten Hochspannungswechselfelds die Dichtigkeit jedes einzelnen Glaszylinders nachgewiesen. Geprüfte, vorgefüllte Fertigspritzen können anschließend dem Montageprozess zugeführt werden. Aus diesen geprüften vorgefüllten Fertigspritzen und weiteren vormontierten Baugruppen entsteht letztlich der Autoinjektor. Endmontage und Etikettierung sind in einer kombinierten Maschine vorgesehen. Nach abschließender Prüfung und Freigabe durch den verantwortlichen Apotheker erfolgt die Auslieferung des gefertigten Autoinjektors in einer geeigneten Versandverpackung.
Alle hier erwähnten Maschinen werden derzeit im Zuge der laufenden Umbauphase eigens konstruiert und gebaut. Ihre äußeren Dimensionen sind dabei so groß, dass die Räume entsprechend der Ausgestaltung der Maschinen realisiert werden müssen. Die Herausforderungen für die Etablierung einer vorschriftenkonformen Sterilherstellung liegen nicht nur im eigentlichen Herstellungsbereich, sondern auch in den technischen Anlagen dahinter, die neben reinraumgerechter Lufttechnik die Versorgung mit einer Vielzahl von Medien sicherstellen (u. a. Druckluft, Stickstoff, Unterdruck, Reinstdampf, Kühlwasser, pharmazeutische Wässer). Da es sich um den Umbau von Bestandsräumlichkeiten handelt, ist in Ulm nicht nur der Aufbau neuer Technik, sondern auch der Rückbau der nicht mehr benötigten Alttechnik erforderlich. Für jede der oben genannten Maschinen sind zudem im Laufe der Konstruktionsphase tausende von Mustern herzustellen und zu liefern, um die pharmagerechte Ausführung auf Industriestandard zu gewährleisten.
Mit Abschluss der Infrastrukturmaßnahme und Übergabe der Räumlichkeiten ist nach derzeitiger Planung Anfang 2024 zu rechnen. Die Maschinen zur Herstellung von Autoinjektoren sollen zu diesem Zeitpunkt betriebsbereit zur Verfügung stehen, um die eigentliche Prozessetablierung zum Abschluss führen zu können. Bedingt durch bereits angedeutete regulatorische Zwänge ist das Ende der Infrastrukturmaßnahme jedoch keinesfalls mit dem ersten Auslieferdatum von Autoinjektoren gleichzusetzen. Maßgebende Meilensteine für die Erstauslieferung von Autoinjektoren sind die Erteilung einer Herstellungserlaubnis durch die zuständige Behörde, den Arzneimittelüberwachungsbeauftragten der Bundeswehr, und einer arzneimittelrechtlichen Zulassung durch das Bundesinstitut für Arzneimittel und Medizinprodukte (BfArM).
Wehrmedizin und Wehrpharmazie 1/2023
Oberfeldapotheker Dr. A. Rohe
Bundeswehrkrankenhaus Ulm
Oberer Eselsberg 40
89081 Ulm
E-Mail: [email protected]